Plaster. This single, solitary word in the old house vernacular elicits a visceral reaction of sorts in many people. It's a characteristic trait of buildings from 60 years to much much older that embodies the true nature of love/hate relationships among DIYers, renovators, preservationists, rehabilitators, flippers, home inspectors, and pretty much anyone who has every worked with the stuff. But interestingly enough, where any one of those people falls in proximity to the seemingly moral thin red line of "rip it out" versus "repair, don't replace," well, that's all based on the relationship you've developed with the walls and ceilings of the past.
When we moved into our house we had been indoctrinated by countless television shows and contractor horror stories in dealing with the fragile, crumbling, dusty, and gritty mess that tends to represent old fashioned plaster. And I'm not going to lie. When we started to think about our home renovation plans, the initial thoughts that our cracked, bumpy, and crumbling plaster was "too far gone" and the belief that we'd need to "gut every room" entered into our conversations quite frequently. But that was before we understood. Before we knew better. Before we shook off the propaganda I'm rather certain started with the gypsum board industry, much the same way vinyl window salesman have long peddled the theory that a home's 100+ year old windows should certainly be removed in favor of energy efficient gems that cost a pantload and "should last a good 30 years." Oh, what a bargain...right?
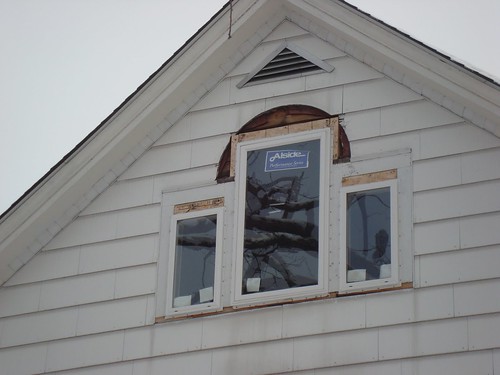
North by Northside, Jeff SkrenesNorth by Northside, Jeff Skrenes
In reality, when you hear the phase "that house has good bones," it's giving a sense of humanity to a building. The bones are represented by the framing and structural items, but one needs more than "good bones" to have a human who is worth anything. In an old home let's be sure to look past the "bones" and see that the plumbing is the circulatory system, the electrical is the nervous system, windows are the eyes, HVAC is the respiratory system, and the plaster and lath walls covering most interior surfaces, well, that plaster is your home's skin. And we all know that the skin is the single most important organ the body owns.
As we learned more about our home's plaster in our early days of renovation, we learned what a truly significant aspect of our home is represented by its original horse hair plaster that still covers the majority of the walls and ceilings. Not only does it offer a basis for wall and ceiling covering, it also provides a unique texture to the interior of our home that drywall board doesn't provide. Slight imperfections, a gentle hand laid roll to the surface, and the noise canceling characteristics of solid, one inch thick or wider plaster adds to the ambiance of any old home, and to lose that, well, you begin to lose the soul of the house.
The result of our education in plaster is a deep seeded desire to salvage and repair plaster whenever possible. It's less invasive, more environmentally friendly, cheaper (from a DIY perspective), generally cleaner (though cleanliness is all relative), and maintains the historic character that is too easily lost in homes today. We've covered how we use plaster buttons to secure our sagging ceilings and cracked walls, as well as how we use a mix of drywall, joint compound, and patience to patch holes left in the plaster by various projects, but we've never really covered a major project dealing with repairing old plaster and mixing in new materials on a much larger scale. Well, that is, until today when we kick off a multi part post on how to achieve this very thing.
We've been working on the walls and ceiling in the bathroom, trying to bring the room back into respectable shape while working to preserve as much of the original fabric of the room as possible. But in our bathroom we have a mix of original plaster, plaster patches, and drywall patches on the ceiling, and drywall on the walls (someone removed all of the wall plaster long before we ever set foot in our home). Our goal is to bring our cracking, sagging, and ugly plaster ceiling back from the brink, while also making sure the drywall on the walls still has that character building hand laid plaster look to it. And we want to do it all in a DIY manner, without breaking the bank, and without wanting to kill ourselves due to the level of difficulty. Easy enough?
When we started this whole thing the plaster on the ceiling was textured and in bad shape. Most contractors or homeowners would look at this as a lost cause and move right into ripping the whole thing down. But not us, no way!
Instead, we began our typical process to repair and revive. We systematically went around the room applying plaster buttons at one foot intervals along the ceiling joists. The idea behind this is simple. Gravity has likely had its way with the ceiling over 100+ years, and the heavy plaster has slowly either pulled away from the wood lath behind it, or it's begun pulling the lath nails right our of the joists. Placing the buttons along the joists pulls the ceiling back up into a stable location. I like to use 2" or 2-1/2" drywall screws for screwing into the joists.
If you're doing something similar, and you notice a lot of sag in any particular area, beef up the number of buttons you're using. Place them every six inches or so to make sure there's something sturdy to pull against.
Once the joists are buttoned, then move on to areas with significant cracking or failing plaster. These areas only have the lath behind it, but the plaster keys (the part of the plaster that pushed through the lath before drying) have often failed, leaving the ceiling or wall unstable. Though the plaster is no longer secured to the lath, you can still use the lath as support for the fix. For these, I like to switch to 1-1/4" drywall screws, since there's only a need to screw into the lath.
There are two major keys here:
- Make sure you're screwing the plaster button into the middle of a piece of lath, otherwise the lath will likely crack and will not offer any support. It's sometimes necessary to guess wrong before you can guess right, so don't worry about trying a few spots.
- Make sure you only tighten the screw to the point where it fully grabs. If you over tighten the screw, it will easily strip the hole in the lath and you'll lose almost all of your support.
Surround the crack, hole, or otherwise failing area with lots of screws and buttons to fully support the fragile plaster areas. You can also use the lath as backer for screwing in drywall patches cut to the size of the hole. Since plaster tends to be about a half inch thick in our house, it's almost perfect to just put in a half inch piece of drywall to fill the hole.
Once you've used about double the number of buttons you think you should have used, and your giant holes or missing plaster have been patched with your material of choice, you're in pretty good shape and can move onto the next step of applying your first layer of skim coat.
It's important to understand how plaster, no matter how many buttons you use, will continue to move as time goes on. Any cracks already in the plaster can be patched, but unless you stabilize the top coat and isolate it from the problem area, you'll end up with cracks in the wall again as normal expansion and contraction occur. This is the reason this next step is so critical.
I prefer to use the brown bag setting type joint compound for my skim coating. You can use the pre-mixed bucket, but it tends to set up softer and therefore can incur dings and divots more easily. Also, using the pre-mix in a bathroom isn't a good option because the moisture of the room can activate the mix after it's already cured.
Purists and preservationists state that you should only use lime based plaster for any skim coating over plaster, and that using joint compound is similar to committing an act of treason. In some respects, they are absolutely right. Lime plaster should only every patch lime plaster. If you have plaster walls and are able to either strip all paint and/or wallpaper exposing the bare plaster, absolutely and 100%, only use hydraulic lime based plaster.
But for us, our plaster is a mish-mash of layer after layer of paint, patched drywall areas, and who knows what else. Now that we've been at this for many years, and we've been using joint compound all along, we see no signs of failure, cracking, or peeling that would make us think we shouldn't keep right on doing what we're doing. However, each case is unique, so please don't take our experience as a definitive "how to" on correcting each and every plaster problem. If we're ever in another house with original plaster walls, there's a pretty good chance we'll be using lime plaster everywhere.
Okay, on with the show...
I like to mix up about half a bag of joint compound at a time in a five gallon bucket. This is greatly simplified by using our awesome hammer drill. I've found it works best to add some water to the bucket first, then add about half the amount of joint compound you actually want to mix up. This allows you to mix in more water than you need and gives you a very watery mixture. This is good, because it eliminates lumps and pockets of dry joint compound, then you continue to add joint compound and water, a bit at a time, until you've mixed up enough and feel like you have what you need.
I tend to mix this first bit of compound a little on the looser side. I'd say it's probably most like a cake batter consistency (just don't eat it).
The goal of this first bit of joint compound is to cover every surface in a very quick efficient manner. If you're using the 90 joint compound (as I like to us) you only have about 70 minutes of working time before your mix will start to thicken, and about 100 minutes before it heats up and turns solid.
Using a flat trowel in my right hand and taping knife in my left, I quickly apply the joint compound over the whole ceiling or wall, loading the trowel with the taping knife before spreading it on in one quick movement. Since this is just the base coat to achieve coverage, you don't need to worry about getting it particularly smooth. You're going for even, thin coats.
Once you've covered the area of wall where you need to work, the next step achieves what can be considered the plaster's new isolation layer. Using a roll of fiberglass mesh (we use standard fiberglass window screen in 48" x 100' rolls), cut a piece of fiberglass that you'll be able to work with. I find a 4'x4' sheet is about as big as we can reasonably handle at once.
Then, using the taping knife, begin embedding the screen in the still wet coat you just applied.
There is definitely a trick to this step, as you need to make sure you apply the screen evenly in the correct position and without any measurable wrinkles or folds. Any bumps, air gaps, or irregularities may weaken the end result, but will definitely cause an inconvenience and pain in getting a good finished surface. If I'm having a hard time I start to embed just a little bit of the screen using my fingers. You can easily see if it's working when the screen is absorbed into the joint compound.
To achieve the smooth application I like to use the "Union Jack" approach. I start at one edge of the screen and use the taping knife across the entire screen to the opposite side, placing an embedded line right in the middle of the piece of screen.
With the middle of the screen on the wall or ceiling, I begin working with the taping knife from the middle towards the edge, starting with a cross that is perpendicular to that first line.
Again, starting from the middle, I begin making diagonal lines out to the corners, effectively making markings similar to the Union Jack flag.
This tends to reduce the likelihood of any bubbles or folds as I'm only working from the center out. Once the Union Jack is in place, I just work to methodically, always from the center to the edges, to embed the remainder of the of the screen in the still wet joint compound.
To ensure full adhesion, I then go over the whole thing with the flat trowel or large taping knife, eliminating any pockets and smoothing any significant bumps.
At this point I like to keep working on putting up screen in the room until all of the screen is in place. Repeating the process for each piece, I ensure an overlap of at least three or four inches on each piece. You could move onto the next step and start jumping around a bit, but I find that to be too overwhelming.
If it's a large room, you may run out of time on the joint compound before it begins to cure. If that happens, it's important to time your process so you aren't left trying to embed the screen in dry joint compound. Otherwise you'll end up frustrated and with a bunch of built up joint compound that you now have to somehow scrape or sand off.
As you move around the room, there will be holes that need to be cut in the screen (such as for lights or ducts). Don't bother trying to pre-cut those holes. Go ahead and put the screen up on the ceiling and allow it to go over top of the holes. Once you've embedded it in place, come back with the utility knife and cut it away. The screen cuts really easily once in the joint compound, and even easier after the joint compound has had a chance to harden up.
Once you've covered the entire room in screen your first layer is done. Sit back, relax, clean up your tools, and admire your hard work. It doesn't look like much, but you're well on your way to a wonderfully smooth and no longer cracked/falling down wall or ceiling. For us, in our bathroom, we'd lived with the horrible texture on the ceiling, the bad cracks, and the fear that the whole thing could come crashing down at any moment for so long that the look of the screen over the whole ceiling was a marked improvement and gave us a tremendous sense of hope.
In our next post we'll continue covering the process and will fill you in on the next steps in correcting ceiling and wall plaster issues. We'll also touch on the first steps to taking a newly hung drywall wall back in time with our tips for making drywall look like it belongs in a house full of plaster walls and ceilings, all as a DIYer.
What are your thoughts on plaster? Are you in a "do whatever it takes to save it" crowd, or do you tend to the "rip it our and replace it" side of the fence?
We have a whole series of plaster repair/skim coating posts you should check out if you like this or are trying to tackle the same thing. Here's the whole list for convenience:
- Plaster Repair for DIYers - No Need to Rip It Out - this post
- Plaster Buttons to Fix Your Crumbling Ceiling
- Plaster Repair Part 2: Laying a New Brown Coat
- How To Fix Plaster Like a Boss: Sand Baby Sand
- DIY Plaster Repair: We Finally Put the Skim in Skim Coat
- My Skim Coating Nickname is Mr. Smooth - The Tricks I Use to Earn It
- The Final Steps to Perfect Skim Coating